Boost Reinforcement Detailing Accuracy
Whether you’re working on complex infrastructure or standard concrete elements, attention to detail in reinforcement placement is key to structural safety and project efficiency. Check out these 5 practical tips for improving your detailing process and ensuring compliance with Eurocode requirements. Implementing these strategies can help minimize clashes, optimize rebar placement, and reduce errors during installation.
5 detailing tips which can help to improve reinforcement detailing accuracy:
(1) Use actual maximum rebar diameter, not nominal. This allowance is needed to take into account ribs and non-round shape of bars. The maximum diameter is approximately 15% larger than nominal. In TeklaStructures the maximum rebar diameter is defined in rebar_database.inp file in the environment folder;
(2) Make some detailing trials in potentially congested zones to check rebar layering arrangement. Especially this is relevant for the thin precast walls. Layering arrangement can’t be changed without confirmation with designer, as it affects an internal lever arm (capacity), nominal axis distance for fire and crack control;
(3) Accurately consider placement of longitudinal bars in corners of links. Especially this is important for link diameters >=20mm with larger mandrel diameter. The positions 1 and 3 in the picture 1 are convenient to perform in Tekla to group corner bar with bottom or side other bars. However, it is necessary to be careful as for beams position 3 decreases an internal lever arm and crack resistance, in lintel integrated in wall the right position can help to avoid clashes with vertical reinforcement in piers;
(4) It is advisable to provide slightly large concrete cover for the starts/ends of strait bars. Especially in zones between edge molds, for example: piers in precast walls. The cutting tolerance of bars is +/-25mm. It is advisable to shorten straight bars slightly to provide more installation flexibility – ref. picture 2.
(5) If 2 or 3 bars are placed closer than minimum required clear distance between (bar diameter, aggregate size +5mm, 20mm), they should be treated as a bundle with equivalent diameter – cl.8.9 EN 1992-1-1. Exception is 2 bars positioned one above the other with good bond conditions. 4 (but not more) close bars can be treated as a bundle for vertical bars in compression and in lapping zone. Equivalent diameter is larger than diameters of component bars, so longer lap and anchorage length must be provide compare with lap and anchorage lengths for single component bars.
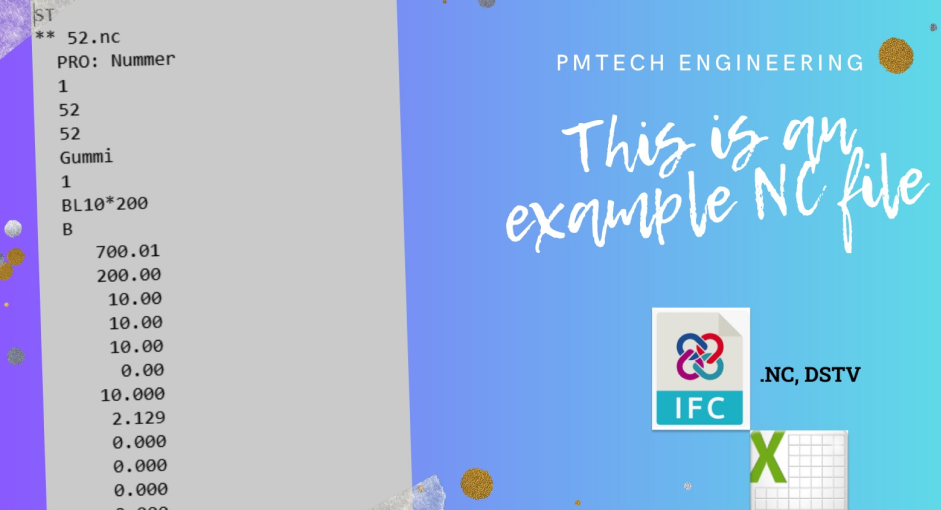
PMtech Engineering can generate CNC data to control automated machinery for fabrication directly
June 23, 2023
CNC (Computer Numerical Control) is a method of automated equipment control used in manufacturing, including milling machines, lathes, laser cutters, and other types of machines.

PMtech Engineering’s scope of work with digital building design
June 21, 2023
Generate output lists by providing intelligent attributes along with 3D information.
Generate quantity lists and bills of materials for all elements.Determine space states.
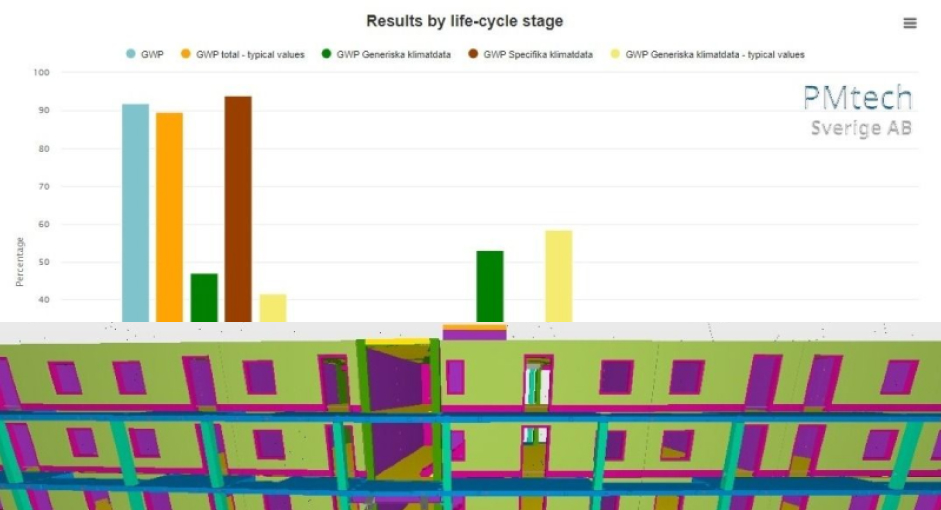
CO2-optimization of reinforced concrete frames
June 6, 2023
In our projects we are strongly committed to the values of sustainable development and environmental policy in all our projects. From early stage consultations to CO2 optimization.